高頻淬火機床作為金屬表面強化的關鍵設備,通過高頻感應加熱與自動化控制的深度融合,實現(xiàn)了零件表面硬度與芯部韌性的精準調(diào)控。以下從設備架構、技術優(yōu)勢、應用場景及智能化升級等方面,全面解析其在現(xiàn)代制造業(yè)中的核心價值:
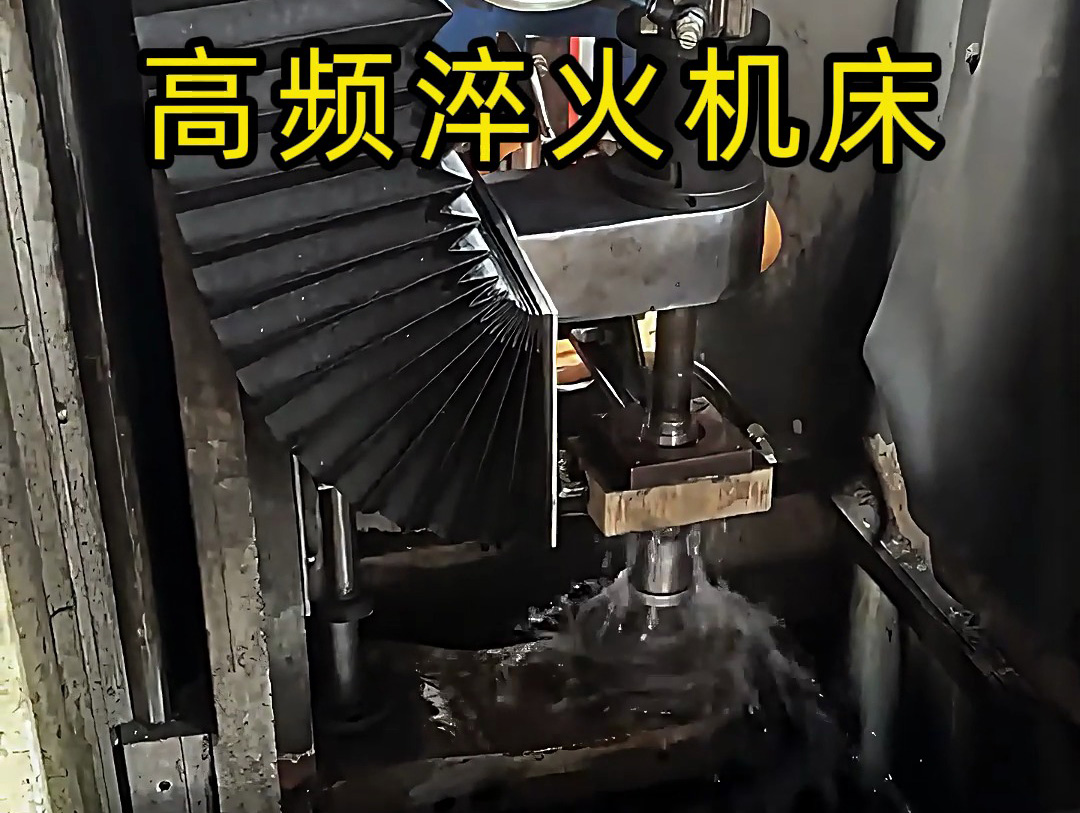
高頻電源系統(tǒng)
旋轉(zhuǎn)盤與工位設計
智能冷卻系統(tǒng)
水基淬火液(PAG 濃度 5-20%),冷卻速度 50-200℃/s 可調(diào);
油冷系統(tǒng)(淬火油閃點≥200℃),適用于變形敏感工件(如精密齒輪)。
淬火介質(zhì)控制:
溫度閉環(huán):紅外測溫儀實時反饋工件表面溫度(精度 ±2℃),動態(tài)調(diào)節(jié)冷卻時間與流量。
PLC 控制系統(tǒng)
電磁感應機制:
高頻電流通過感應線圈產(chǎn)生交變磁場,工件表面激發(fā)渦流生熱(公式:P=Kf2B2σ,P為功率密度,f為頻率,B為磁感應強度,σ為電導率),加熱速度可達 100-200℃/ 秒。
集膚效應應用:
通過調(diào)節(jié)頻率控制加熱深度(δ=5030/f?ρ?μr),如 45# 鋼件頻率 200kHz 時,硬化層深度 0.5mm;頻率 20kHz 時,深度 2.5mm。
維度 | 高頻淬火機床 | 傳統(tǒng)箱式爐淬火 | 火焰淬火 |
---|
加熱速度 | 秒級(10-30 秒) | 小時級(1-3 小時) | 分鐘級(5-10 分鐘) |
硬化層精度 | ±0.1mm | ±0.5mm | ±0.3mm |
能耗 | 0.5-1.5kWh / 件 | 5-10kWh / 件 | 2-5kWh / 件 |
人工依賴 | 無需持證技工 | 需熱處理技師 | 需熟練操作工 |
環(huán)保性 | 無油煙、低輻射 | 油煙排放 | 有害氣體排放 |
型號 | 功率 (kW) | 頻率 (kHz) | 工位數(shù)量 | 適配工件尺寸 | 典型行業(yè) |
---|
HT-C6-60 | 60 | 20-200 | 6 | 齒輪 m≤5,軸≤φ100mm | 汽車零部件 |
HT-C12-120 | 120 | 5-100 | 12 | 齒輪 m≤8,軸≤φ200mm | 工程機械 |
HT-C20-200 | 200 | 5-50 | 8 | 大型齒輪 / 軸類 | 重型機械 |
設備投資:150 萬元(含機械手)
年產(chǎn)能:20 萬件
成本節(jié)約:
人工成本:減少 4 名技工,年節(jié)約 28 萬元;
能耗成本:較箱式爐節(jié)約 70%,年節(jié)約 12 萬元;
廢品成本:不良率下降 10%,年節(jié)約 20 萬元;
投資回收期:約 24 個月
電源模塊:每季度檢測 IGBT 溫度(≤75℃),每年更換散熱硅脂;
冷卻系統(tǒng):每月清洗噴嘴(防止淬火液結(jié)晶),每半年更換過濾芯(精度 5μm);
旋轉(zhuǎn)機構:每季度潤滑軸承(使用鋰基脂),確保旋轉(zhuǎn)噪音≤75dB。
綠色淬火介質(zhì):開發(fā)生物可降解淬火液(如淀粉基聚合物),COD 排放降低 90%;
增材制造集成:淬火與激光熔覆結(jié)合,實現(xiàn)磨損零件的快速修復(如曲軸局部硬化層再生);
量子傳感應用:量子點紅外探測器(精度 ±0.1℃)實時監(jiān)測納米級溫度分布,推動微觀組織精準控制。
高頻淬火機床通過 “感應加熱的高效性 + 自動化的穩(wěn)定性 + 智能化的精準性”,重塑了金屬熱處理的技術邊界。從汽車齒輪的大批量生產(chǎn),到航空航天精密零件的定制化加工,其卓越表現(xiàn)正在推動制造業(yè)向 “少人化、高精度、低碳化” 轉(zhuǎn)型。對于企業(yè)而言,選擇高頻淬火機床不僅是設備的升級,更是生產(chǎn)模式的革新 —— 讓每一次淬火,都成為零件性能躍升的起點,讓熱處理工藝,成為核心競爭力的重要支撐。
技術洞察:隨著 “雙碳” 目標推進,高頻淬火的低能耗特性(較傳統(tǒng)工藝減排 60% 以上)將成為市場準入的關鍵指標,提前布局智能化高頻裝備,即是搶占未來制造業(yè)的綠色制高點。